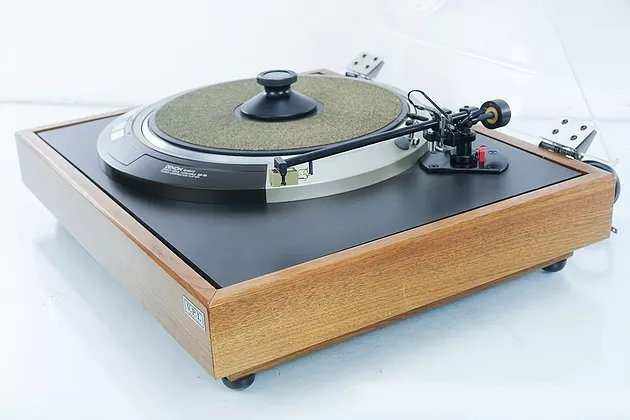
October 21st, 2018 (Archived 10/21/2018)
Share
Brief History (Excerpts from the VPI Book)
In the late 70’s Harry Weisfeld started creating accessory components for his Audiophile hobby. Coming from an Electrical Engineering background he was fascinated with Direct Drive turntables. Harry enjoyed making accessories in America that could help improve the listening experience. One of those accessories was the HW-9 isolation base which was made specifically for the Denon DP-75 with a mounted gimbal tonearm. (Pictured above)
As a milestone in the foundation of VPI, it was a goal to develop and produce a Direct Drive turntable to pay tribute the company design roots. Harry with his wife Sheila, who ran the office for over 30+ years, continued to develop and grow VPI. This is highlighted through milestone products such as the HW-16, HW-19, TNT, Aries, Scout, and Classic turntable.
In 2012 VPI continued with their son Mathew Weisfeld who brought new ideas and approaches to the company. Adding his experience with CAD and computer technology VPI incorporated 3D printing into their designs. The VPI Prime becasue Mat's milestone product. Mat with his wife Jane continued in his parent’s footsteps of quality products Made in America.
With the help of proven Electrical Engineer Michael Bettinger VPI and the rest of the VPI team the HW-40 came into existence.
HW-40 Anniversary Table
-
The HW-40 Direct Drive is an evolution of VPI’s 40-year design and engineering while holding the DNA of our Class A+ Classic Direct design.
-
Retaining our initial Direct Drive motor design and benefiting from the best of 2018 motion control circuitry/software; vibration and isolation technology;
-
The chassis is made from solid machined .7500 thick 6061 aluminum finished with a textured black with an internal dampening plate.
-
Every part mounted with machined screws into blind tapped holes for a clean and sleek look/design.
-
Removable machined aluminum arm-board.
-
Beautiful limited-edition gloss wood sides.
-
Start, 33, 45 buttons.
- All power supply and controls circuitry internal, no added-on boxes or power supplies.
-
Removable platter for easier shipping.
-
Removable hinged Dust Cover.
-
The 12" gimbal 3D printed Fat-Boy arm with triangular to circular resonance canceling design. The robust gimbal bearing used ABEC 9 bearings made in Japan for ultra-low friction.
-
The tonearm uses an adjustable threaded counterweight for accurately fine tuning your VTF setting.
- New Fat-Boy VTA design with a smoother and more robust adjustment machined aluminum and steel knob.
Motor control feedback and firmware
Motor speed feedback utilizes a ring encoder providing 2500 pulses/revolution, monitored by cutting edge motion control software and motor drive circuitry. The motor control programming utilizes the same hardware/software used in many state-of-the-art/precision manufacturing tools and inspection systems.
Platter rotation feedback provides 2460 pulses per revolution to allow precise monitoring of both the velocity, position of the platter/motor while playing a record. The combination of high torque and high-resolution feedback, provides a solid dynamic response from the motor driver to the varying demands of the stylus while tracing the record grooves.
The musical effect is one of smoothness and lack of congestion during complex passages allowing the various components buried within a recording to remain separate and unaffected by the other instruments and other artifacts of the recording. The impression is that a fine signal-related texture has been removed from the music. The improvements in the rhythmic drive is similar to the effect of a rim drive only better.
Motor Tuning
The motion control software used in the HW-40 normally finds itself in machines where high accuracy, fast motion of high mass machine components is required. The software presents the capability of not only controlling the speed accurately but adds the ability to fine tune how the corrections are applied and minimize the effects of vibration and noise generated by the servo drive power to the motor.
The fine tuning of the motor drive was accomplished through using a combination of the pallet of capabilities within the software and a tuning process that monitored the output of the table itself while playing unmodulated groove test records and evaluating the effects of tuning options. The goal being to minimize/eliminate any perceptible evidence of the motor drive signal. The end result is a dead quiet presentation and retrieval of subtle details buried in the recordings.
Speed stability was evaluated musically with a large selection of known quality recordings of vocals, strings, pianos, room effects and decays for any evidence of instability during the tuning process. The speed stability of the HW-40 is beyond the capabilities of the many fine speed test records in our collection.
Vibration control
Managing the isolation of a table of this caliber is normally left to external isolation racks and platforms. Not only is the challenge of isolating a table of this size (mass) from the energy in the room a challenge, isolating the platter /tonearm system from motor and internal table excited vibrations is also a challenge.
The isolation system incorporated into the HW-40 direct drive is the product of two years of development. It incorporates a combination mass loading/ mechanical stiffening, selective damping and skillful combinations of elastomers to isolate the table and cartridge from the physical world around it.
Construction quality and reliability
To insure long term reliability and performance all component parts used in the HW40 are spec'd to be used in high reliability equipment, equipment meant to be put into operation and run 24/7 for years. Circuit components are sourced from major industrial electronics suppliers with solid track records for consistency and reliability. The core components, motors and drive electronics have been in constant use since the first prototypes of this design came to life.